
Controlling the unsteady bonding temperature
OTOMcomposite presents an effective process optimization methodology for AFP of complex part geometries by means of a numerical optical-thermal model. A winding path on a pressure vessel’s cylindrical and ellipsoidal (dome) part is considered with varying tooling curvature. The maximum laser intensity increases by approximately 80% and the process (bonding) temperature changes by 80 °C at the intersection of the cylindrical and dome section of the pressure vessel. The conducted optimization methodology regulates the temperature within 1.5 °C variations with respect to the desired value. In order to compensate for the transient local curvature effects on the process temperature, the total laser power varies between 30% and 175% of the reference (non-optimized) case.
The graphical and benchmark effects are represented below:
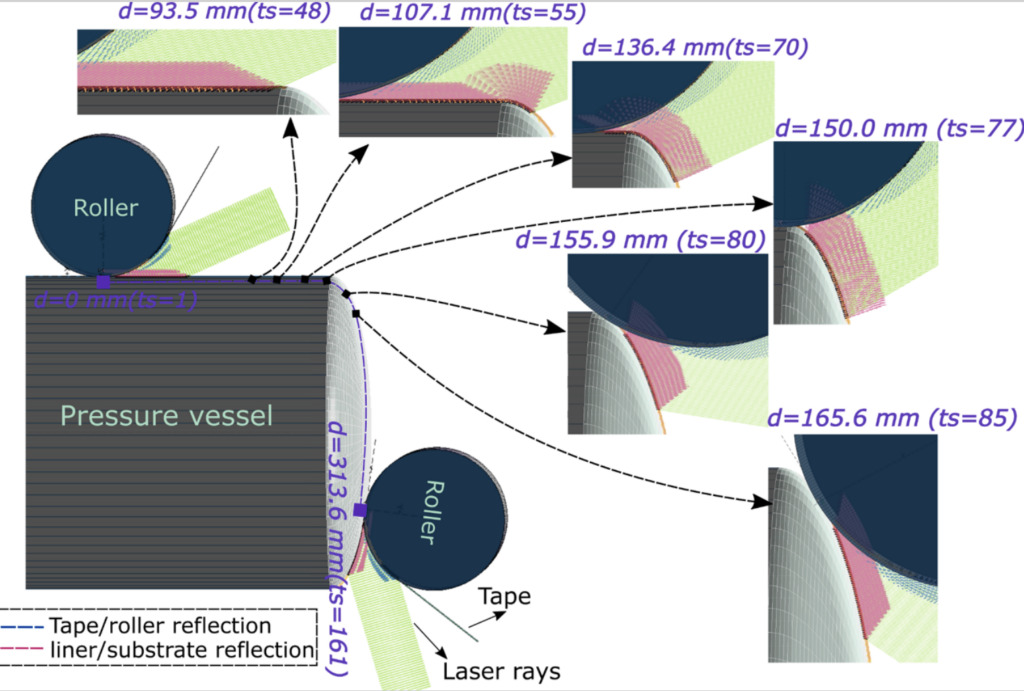
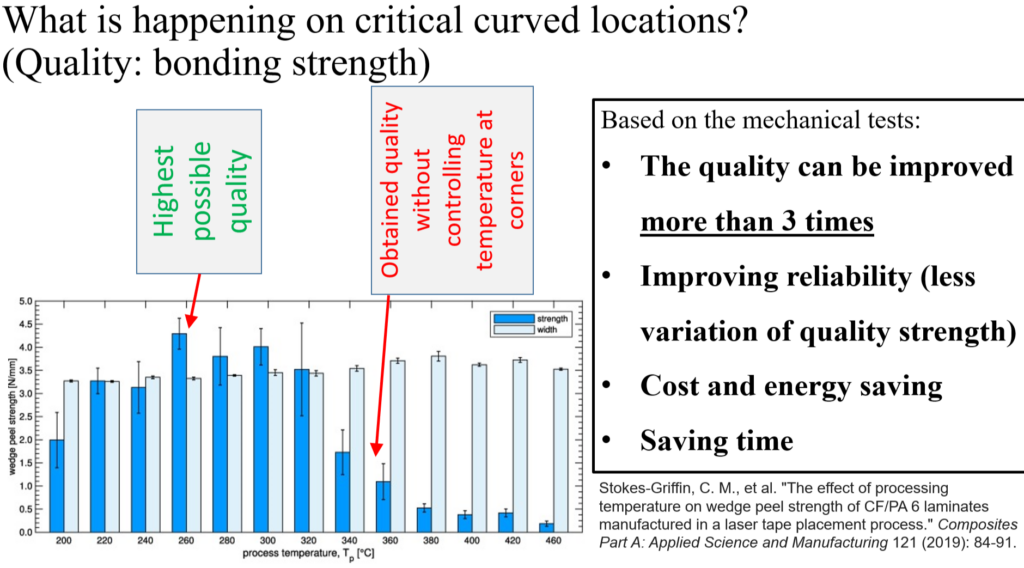