-
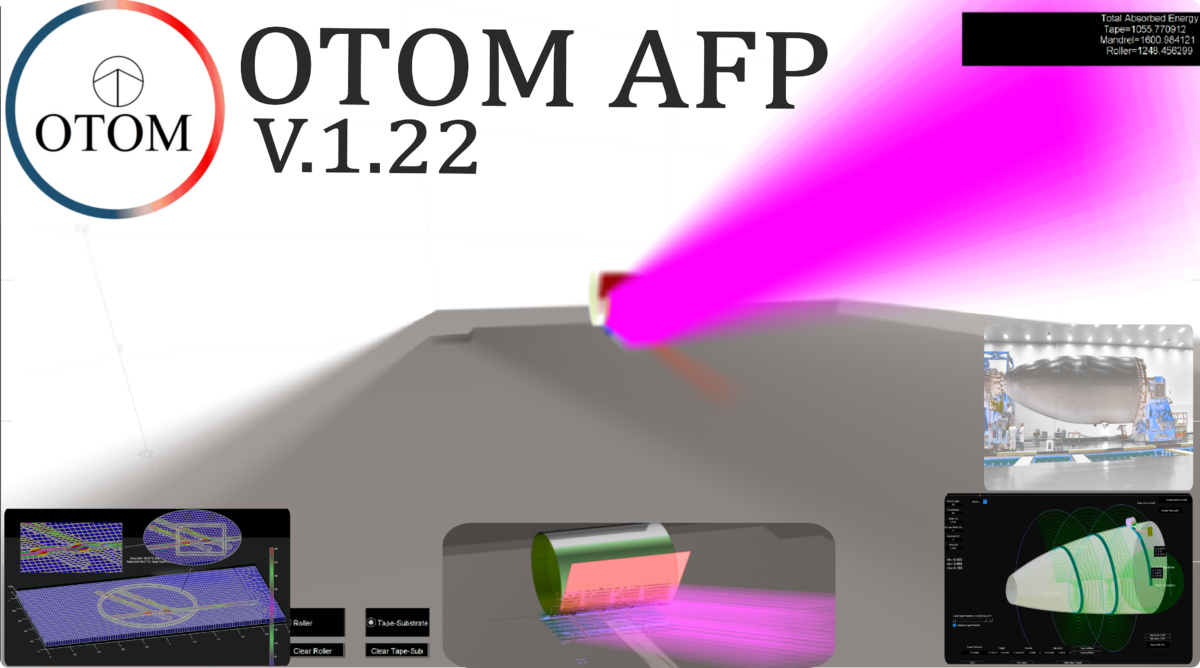
OTOMcomposte developed novel techniques for the additive manufacturing simulation process.
In the context of modeling the automated fiber placement (AFP) process using a numerical finite element (FE) model and optical ray tracing, the method involves discretizing the boundary conditions. Here is an overview of the approach:
Geometry and Material Definition: Start by creating a geometric representation of the component or structure being manufactured using automated fiber placement. Define the material properties, such as the mechanical behavior and optical properties, which are crucial for the simulation.
Finite Element (FE) Modeling: Employ an in-house numerical FE model that represents the physical behavior of the component during the automated fiber placement process. This model incorporates mechanical properties, such as stiffness and thermal behavior, as well as specific boundary conditions.
Discretization of Boundary Conditions: Discretize the boundary conditions by defining the necessary parameters for the Additive manufacturing simulation. This involves specifying the input parameters for the automated fiber placement process, such as the fiber path trajectory, deposition rate, temperature profile, and pressure distribution. The boundary conditions will vary depending on the specific process and the properties being analyzed, such as thermal analysis, stress analysis, or optical analysis.
Optical Ray Tracing: Integrate optical ray tracing techniques into the FE model to simulate the interaction of light with the composite material. This allows for the analysis of optical properties, such as light transmission, reflection, and refraction, during the manufacturing process. Optical ray tracing can provide insights into the curing process, optical distortion, and the behavior of the composite material with respect to light.
Simulation and Analysis: Run the numerical simulation using the FE model and optical ray tracing techniques. Analyze the results to gain insights into the behavior of the AFP process. This may include evaluating factors such as fiber alignment, thermal gradients, stress distribution, curing quality, and optical performance.
By discretizing the boundary conditions, combining FE modeling with optical ray tracing, and utilizing appropriate numerical methods, it becomes possible to simulate and analyze the AFP process, allowing for optimization and improvement of the manufacturing process.